Numerical Simulation of Radial Fretting Behaviors Using Ball-Plate Model
-
摘要: 通过径向微动的数值模拟,研究了径向微动磨损过程中的力学行为和损伤机理.以球(Si3N4)-平板 (VitaMarkII)模型为研究对象,通过Hertz理论分析,得到球和平板的接触半径、法向分布力之间的关系.应用 Ansys软件建立有限元模型,计算得到接触表面的应力、应变和滑移分布.研究结果表明:滑动区摩擦因数对粘 着区应力、应变影响不大,但对滑动区应力、应变、滑移量造成的影响比较明显,必须考虑;采用弹性模量和泊松 比相近的材料为对摩副时,可减小相对滑移量,降低磨损;在滑动区,特别是在接近接触边缘区域,滑移量较大, 与实验结果吻合.Abstract: A ball-plate model and the Hertz theory were used to determine the relation between distributed forces and the contact radii on a Si3N4 ball and a Vita Mark II ceramic block. A finite element model was derived to determine the distribution of stress, strain and sliding. The simulation results are practically consistent with test results reported by somebody else. The friction coefficient in the sliding area has a little effect on stress and strain in the stick zone, but its effects on stress, strain and sliding are not neglectable in the sliding zone. Friction pair materials with similar elastic modulus and Poisson's ratios are desirable for reducing relative sliding and wear. Significant sliding appears in the sliding area, and the largest sliding appears near the outer edge of the contact zone.
-
Key words:
- radial fretting /
- fretting wear /
- contact stress /
- Hertz theory /
- ball-plate model
-
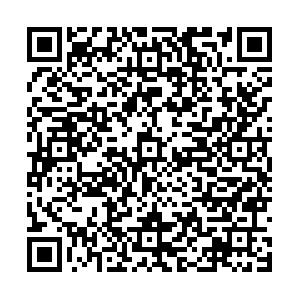
计量
- 文章访问数: 1445
- HTML全文浏览量: 92
- PDF下载量: 628
- 被引次数: 0